Grasping the Art of Welding: How to Prevent Undercut Welding Issues for Flawless Fabrication Results
Efficiency and accuracy are paramount worldwide of welding, where also the least imperfection can compromise the structural integrity of a made item. One typical challenge that welders face is undercutting, an issue that can lead and damage a weld joint to pricey rework. By comprehending the source of undercut welding and executing effective techniques to stop it, welders can elevate their craft to brand-new levels of quality (Preventing weld undercut). In the quest of remarkable fabrication results, understanding the art of welding to stay clear of undercut concerns is not simply a skill yet a need for those aiming for perfection in their job.
Understanding Undercut Welding
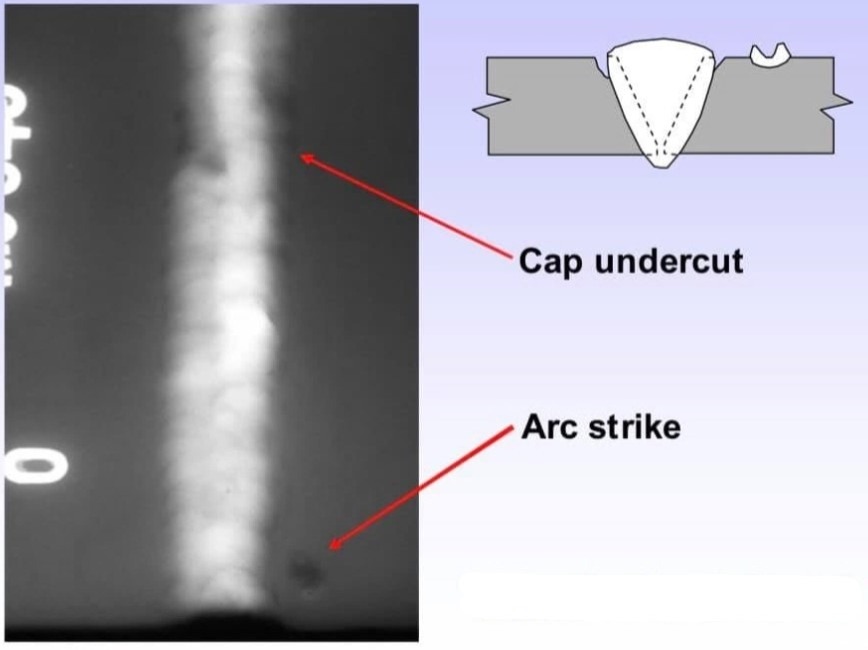
To protect against undercut welding, welders must guarantee proper welding parameters, such as readjusting the existing, voltage, travel rate, and maintaining the right electrode angle. By comprehending the causes of undercut welding and implementing precautionary measures, welders can accomplish high-grade, structurally audio welds.
Sources Of Undercut in Welding
Recognizing the aspects that add to damage in welding is vital for welders to generate top quality, structurally audio welds. Poor welding existing or wrong welding speed can likewise add to damage. Understanding these causes and carrying out appropriate welding methods can help prevent damaging problems, ensuring solid and durable welds.
Strategies to avoid Undercutting

To mitigate the danger of undercutting in welding, welders can use strategic welding techniques focused on enhancing the quality and integrity of the weld joints. One reliable approach is to adjust the welding parameters, such as voltage, current, and travel rate, to ensure proper warmth input and deposition. Preserving a suitable electrode angle and guaranteeing constant traveling rate can also help avoid undercut. In addition, utilizing the appropriate welding technique for the certain joint setup, such as weave or stringer grains, can add to minimizing damaging. Preventing weld undercut.
In addition, correct joint preparation, including ensuring tidy base materials free of pollutants and using the proper welding consumables, is important in protecting against undercut problems. Utilizing back-step welding methods and managing the weld grain profile can also aid distribute warm uniformly and minimize the risk of undercut. Routine examination of the weld joint throughout and after welding, along with implementing top quality guarantee steps, can assist in addressing and detecting undercutting concerns immediately. By implementing these methods carefully, welders can accomplish remarkable manufacture results with minimal undercut issues.
Value of Correct Welding Criteria
Selecting and preserving suitable welding specifications is vital for attaining effective welds with marginal flaws. Welding specifications refer to variables such as voltage, existing, take a trip speed, electrode angle, and protecting gas circulation rate that directly impact the welding procedure. These specifications must be carefully adjusted based upon the type of material being welded, its density, and the welding strategy utilized.
Correct welding specifications guarantee web link the appropriate quantity of warmth is applied to melt the base steels and filler material uniformly. If the additional reading parameters are established too expensive, it can result in extreme warmth input, triggering distortion, spatter, or burn-through. On the various other hand, if the criteria are also low, insufficient combination, lack of infiltration, or undercutting may happen.
Quality Assurance in Welding Procedures

Conclusion
In final thought, mastering the art of welding requires an extensive understanding of undercut welding, its causes, and techniques to stop it. By ensuring appropriate welding parameters and executing quality control practices, remarkable manufacture results can be achieved. It is vital for welders to constantly pursue excellence in their welding procedures to prevent undercut issues and generate premium welds.
Undercut welding, a common defect in welding processes, happens when the weld metal does not effectively load the groove and leaves a groove or anxiety along the welded joint.To prevent undercut welding, welders need to make sure correct welding criteria, such as adjusting the present, voltage, travel speed, and maintaining the appropriate electrode angle. Inadequate welding incorrect or current welding speed can likewise add to damage.To mitigate the threat of try this site undercutting in welding, welders can employ strategic welding methods aimed at boosting the high quality and integrity of the weld joints.In conclusion, mastering the art of welding requires a complete understanding of undercut welding, its reasons, and strategies to avoid it.